Safety and Quality
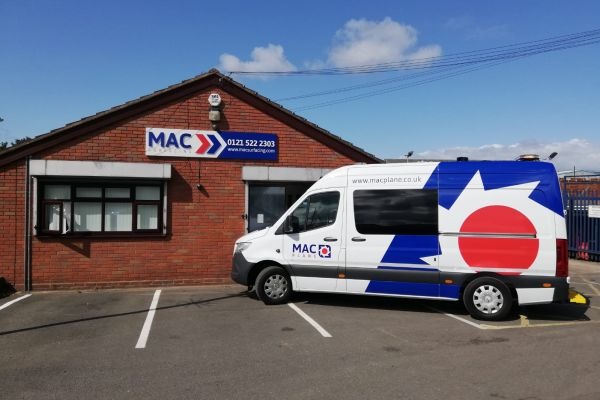
Safety and Quality
Safety and quality should be amongst the pillars of any business - especially one that other companies are reliant on to deliver, excel, and in some cases - survive.
MAC PLANE prides themselves on safety and quality values, with a strong operational back office, 24/7 availability, in house fitters and a mission to keep ensuring that MAC Plane is a contractor to rely on, nationwide.
This impressive setup and operational capability have seen essential works carried out supporting local authorities such as Stoke on Trent and Staffordshire County Council, M6 Toll, HE Areas 2, 7, 9, 10 and 12 as well as patching works for private contractors in Buckinghamshire and Cheshire to name just a few.
So, how does MAC PLANE showcase their approach to safety?
Firstly, the company is a member of Safeplane (Federation of Planing Contractors) which sets common safety standards for members to follow. For example, Banksman with certain size machines that fall part of a risk assessment, as well as safety communication headsets.
The company utilises modern equipment and implements the latest safety initiatives, with examples including safety exclusion zones around planers - which is also becoming common practice across the entire highways sector when it comes to people-plant interface.
MAC PLANE also implements an extensive continual training programme, ensuring that their experienced operators are trained to a standard of CSCS with NVQ Level 2, Plant Certification for appropriate planer size and relevant safety qualifications such as first aid, and all training is regularly refreshed and kept up to date with latest industry standards.
The industry often requests critical safety medical certificates as common practice now, and MAC PLANE ensure all operatives are in possession of such certificates, and any concerns are always monitored by a manager.
Regular safety audits are carried out by the in-house management team and an external consultant and are communicated with clients where possible. Two active MAC directors also hold the Nebosh General Certificate in Occupational Health and Safety which demonstrates the MAC PLANE passion and commitment to keeping their workforce safe.
So that's safety, what about quality?
MAC PLANE prides themselves on only employing the best operators in the industry. MAC PLANE has a passion for quality, and this is demonstrated by everyone they send to site.
To ensure delivery, MAC PLANE runs machines with backup engines to ensure that if anything was to fail, the machine can continue to run, and the show can go on. Additionally, MAC PLANE is overseen by Ian Hitchborne - an experienced planing manager that understands the demands and needs of the industry, and not just the MAC PLANE business.
Costs aren't everything. Read that again: Costs. Aren't. Everything. Working with renowned machine manufacturer, Wirtgen and established pick manufacturer, Betek, MAC PLANE invests in the highest quality machinery and doesn't look for the cheapest option. Focusing on quality over cost pays real dividends with the overall quality of jobs delivered by MAC PLANE.
MD Marc Copson spoke to us about some of MAC PLANE's other quality:
"Being supported by an established hire-based surfacing business means that we can adapt to a customer's requirement, rather than viewing every job as 'one size fits all.'"
"Additionally, thinking about our clients, we focus heavily on legal compliance across the whole business, and this means that our clients risk considerations can be low when utilising MAC PLANE."
With a team of experienced fitters, the MAC stamp of quality can be assured.
The in-house workshop based in the West Midlands is supported by mobile fitters nationwide. MAC PLANE's established relationships with manufacturers are set to provide external support when needed.
Marc added:
"We deliver a "Wirtgen trained" training programme to ensure our fitters understand everything about the machines we operate- leaving no stone unturned in their learning and skills development.
The in-house workshop is handled by a workshop manager and is running all year with 5 full time fitters and provides 24/7 cover - a workshop fitter is quite literally on call every day of the year."
And how is this quality delivered? What about the back-office network of support?
MAC PLANE operates their delivery via state-of-the-art IT resource planning technology, custom built in house - this is a major advantage over the competition given this is the real brains of their operation, and it isn't available off-the-shelf.
On the back office, Marc continued:
"Our strong back office team knows the industry from all angles and being supported by a hire-based surfacing business, our MAC PLANE team really understand the needs of our client and problems they face when dealing with independent planing contractors.
"Having a strong team means that support is always there to ensure service levels do not drop, and the quality management systems we operate ensure we are focused on the customer.
As a final statement on delivering quality, Marc told us:
"A member of the management team is available 24/7 - and can react to all emergency requirements - whether it is planing or surfacing."